Jakość wbudowana w proces powinna być pochodną podejścia, filozofii „0 Wad” lub bardzo często nawet „0 wad na następny proces”. O sukcesie takiego zarządzania jakością decydują jednak składowe z zakresu efektywnego systemu zarządzania, odpowiednio dobranych narzędzi procesowych, adekwatnych do organizacji i jej problemów wraz z właściwym zarządzaniem ludźmi i budowania wśród nich świadomości i odpowiedzialności procesowej.
Tym samym hasło „Dobrze za pierwszym razem” nie powinno być jedynie wyświechtanym hasłem na tablicach SFM, a faktycznie celem samy w sobie. U jego podstaw powinno leżeć mimo wszystko postawa pracownicza ukierunkowana na brak zgody na przyjmowanie, wytwarzanie i przekazywanie „złej jakości”.

Literatura podaje, iż zmiana „mindsetu” w organizacjach zarządzanych na bazie kontroli, a nie zapewnienia jakości trwa średnio ok.8 lat. I tym samym wymaga jasno zdefiniowanego kierunki, wizji, pod którą należy podciągać całą strategię przedsiębiorstwa. Tyle teoria, w praktyce bowiem wiemy, że w wielu firmach mimo wszystko jest to całkowicie niewykonalne.
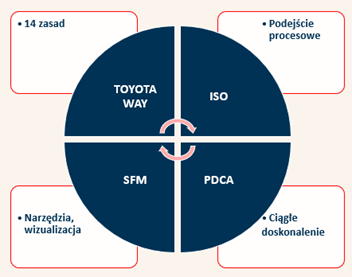
Koncepcja Jakości wbudowanej w proces, może mieć następującą strukturę:
1. Baza 14 zasad Toyoty,
2. Podejście procesowe zgodnie z wymaganiami ISO,
3. Ciągłe doskonalenie
4.Sprawdzone i nieskomplikowane narzędzia, wizualizacja
Baza 14 zasad Toyoty
Z bazy tej wyłania się obraz tzw. 4P Toyoty: Philosophy, Process, People, Problem Solving, a ogólne podejście Toyoty opiera się na dalekosiężnej koncepcji, nawet kosztem krótkoterminowych wyników finansowych.
W zakresie procesów (Process) jest to oczywista eliminacja każdego rodzaju marnotrawstw (MUDA – marnotrawstwo, MURI – przeciążenie pracą, MURA – nierównomierne obciążenie pracą). Dodatkowo krytyczne tutaj jest stworzenie kultury przerywania procesów w celu rozwiązywania problemów, aby od razu osiągnąć oczekiwaną jakość, przy odpowiednio zbudowanej świadomości oraz zastosowania odpowiednich do tego narzędzi.
Ludzie (People) to zazwyczaj niewykorzystany kapitał, a podejście Toyoty w tym zakresie opiera się głównie na wykształcaniu wyjątkowych ludzi i tworzeniu zespołów realizujących ogólną koncepcję firmy, a następnie nauczaniu innych.
I w końcu (Problem Solving), który determinuje osobiste angażowanie się w rozwiązywanie problemów, celem lepszego zrozumienia istniejącej sytuacji. Decyzje przy tym powinny być podejmowane powoli, a działania szybko.

Podejście procesowe zgodnie z wymaganiami ISO. Kolejny proces jest Klientem.
To klasyczne podejście procesowe bazujące na kartach procesów opisujących WE, WY, uczestników, właścicieli oraz KPI. Tym samym ważne jest tutaj określenie również zakresów uprawnień oraz odpowiedzialności i decyzyjności w ramach procesów.
Co ważne, w podejściu tym bardzo często rozumie się również wszystkiego rodzaju czynności kontrolno – pomiarowe zdefiniowane na podstawie oceny ryzyka, skalkulowane, znormowane i wbudowane w zakres prac pracownika produkcji.
I tutaj płynnie następuje przejście do Ciągłego doskonalenia (PDCA), które powinno mieć charakter iteracyjny, naprzemienny wraz z SDCA, czyli standaryzacją. A każda raz powtórzona lub odrzucona hipoteza, po ponownym przeprowadzeniu cyklu powinna się przyczyniać do dalszego rozszerzenia wiedzy.
Sprawdzone i nieskomplikowane narzędzia, wizualizacja
I na koniec zwieńczenie prac w postaci wskazania problemów ich wizualizacji, celem ich rozwiązania. Odpowiednio zebrane i zgrupowane dane, przedstawione w formie wykresów wraz z trendami, przy zastosowaniu kolorów zielony = OK, czerwony = NOK wraz z rozpisanymi Action Plan, to klucz do budowania przynależności do zespołów i ich zaangażowania.