Na Ogólnopolskiej Konferencji Jakościowej w Gliwicach, organizowanej przez „Jakość bez retuszu z Anna Farion” miałem przyjemność i okazję przybliżyć temat optymalizacji cech produktu i procesu ukierunkowanych na spełnienie wymagania klienta. Swoją prelekcję oparłem
o osobiste doświadczenia tak z pracy w korporacji produkcyjnej jak i nabyte prowadząc spółkę Projektownia PPM jako CEO, którą, obecnie reprezentuje.
Konstrukcję prelekcji zbudowałem na planie rzeczywistej sytuacji, w której producent aby spełnić wymagania jakościowe swoich odbiorców decyduje się na zakup nowej maszyny. W tej sytuacji omawiałem wpływ takiego procesu na osiągnięcie celu jakim jest stabilna produkcja o wysokiej jakości produktu.
Przejdę do konkretów. Na początku takiego procesu warto sobie zadać kilka pytań. Proponuję zacząć od pytania „kupuję maszynę czy proces?”. Jeżeli znam procesy swojej organizacji jestem właścicielem know-how będę oczekiwał od nowej maszyny lub stanowiska standardu, który mam, użycia do jej budowy konkretnych komponentów oraz umiejętności stabilnego utrzymania określonych parametrów procesowych, których poznanie wymagało od mojej firmy lat doświadczeń i/lub godzin testów i badań. Pod dyskusję i ewentualnej zmianie zostaną poddane konkretne obszary wskazane do poprawy. Tu możemy płynnie przejść do kolejnego z istotniejszych pytań jak:, „co jest dla mnie ważne w zakupionym towarze, jakie cechy są dla mnie ważne”. Te i im podobne pytania są istotne z punktu widzenia podniesienia innych parametrów nie związanych bezpośrednio z powodem zakupu a niezwykle istotnym z punktu widzenia szeroko rozumianego dobra naszej organizacji i jej rozwoju oraz bycia konkurencyjnym na rynku.
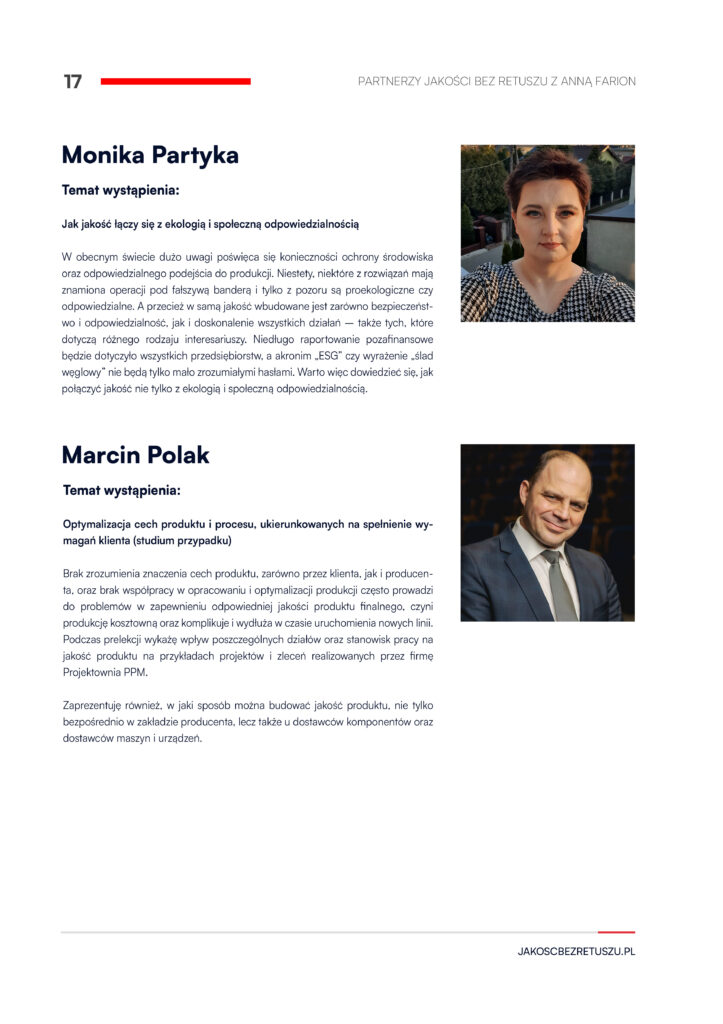
Myślę tu o takich zagadnieniach jak:
1) energochłonność, rozumianą jako ilość energii zużywanej w procesie technologicznym
i produkcyjnym oraz w całym łańcuchu przemian energetycznych przypadająca na jednostkę efektu tego procesu,
2) czas przezbrojeń, zabierający nam cenne minuty produkcyjne a mające coraz większe znaczenie biorąc pod uwagę skracanie się ilości produkcji danej referencji zestawionej z rosnącą wariantowością produktu,
3) ilość narzędzi pod różne referencje.
Tu argumentem za analizą jest:
– brak miejsc na przechowywanie,
– koszty zakupu i utrzymania,
– konieczność organizowania i przeprowadzania kontroli prawidłowego użycia w procesie, czyli zagwarantowania prawidłowego użycia wszystkich narzędzia do produkcji konkretnego produktu,
– mnożenia zabezpieczeń na tych narzędziach czyli kontroli nad zapewnieniem jakości, ale i kosztami,
– dostępności do maszyny podczas produkcji. Mam tu na myśli zadbanie aby serwis mógł się odbywać w sposób bezpieczny przede wszystkim dla obsługi technicznej jak i z zachowaniem ciągłości produkcji. Tu pomoże nam znajomość możliwości odcięcia energii z danej części maszyny lub zespołu maszyn (linii produkcyjnej). Zadbajmy również o to jak będzie przebiegał proces odbioru. Przygotujmy się na niego aby w dniu uruchomienia nie dochodziło do nieporozumień prowadzących do konieczności wprowadzenia zmian. Które na tym etapie są najdroższe i najbardziej czasochłonne. Tu kuszące jest skorzystanie z RFQ innych projektów realizowanych w naszym zakładzie tylko czy samo kopiowanie nam pomoże i pozwoli nam zaoszczędzić czas oraz zoptymalizuje efekt oczekiwany? To pytanie zostawiam otwarte. Doświadczenie wskazuje, iż zamawiający często nie jest świadomy wymagań prawnych, branżowych, konieczności sprostania normom i przepisom wewnątrz zakładowych. Prawidłowe zdefiniowanie potrzeb i wymagań pozwoli na uniknięcie takich sytuacji jak:
– przesunięcia terminów poszczególnych etapów z powodu konieczności wprowadzenia zmian w projekcie, fizycznie na maszynie, stanowisku lub zespole maszyn,
– wstrzymania odbioru i uruchomienia produkcji przez różne działy jak BHP, UR, metrologię czy produkcję a czasami i jednostki zewnętrzne,
– powielania błędów przez nie wyciąganie wniosków z historii produkcji, która często ma swój początek w braku lub niewłaściwie prowadzonej komunikacji wewnątrz poszczególnych komórek organizacyjnych jak i między nimi, co ma przełożenie na ponoszenie dodatkowych kosztów ze względu na konieczność doposażania stanowiska w systemy bezpieczeństwa, czy dodatkowe układy kontroli procesu. Warto skorzystać z takich narzędzi jak FMEA czy DFMA.
Zależało mi aby podczas prelekcji wybrzmiewały takie słowa jak człowiek, multidyscyplinarny zespół, zaangażowanie, bezpieczeństwo i jakość. W moim odczuciu istotą jest zdanie sobie sprawy, iż jakość nie posiada granicy, nie zaczyna się i nie kończy. Jakość nie jedno ma imię, czasami jest liczbą po przecinku, czasem komfortem użytkowania a innym razem sposobem komunikacji i towarzyszącym im emocją. Jakość nie ma jednego odpowiedzialnego, a każde działanie w organizacji ma swoje konsekwencje we wszystkich aspektach jej funkcjonowania. Każdy pracownik ma wpływ na to co opuszcza jego zakład. Każde działanie prowadzi do określonego skutku. Tu chętnie zacytuję „Jeśli ciało A działa na ciało B siłą (akcja), to ciało B działa na ciało A siłą o tej samej wartości i kierunku i przeciwnym zwrocie (siła reakcji). Co dla mnie niezwykle ważne w przekazaniu, to że na początku każdego działania jest człowiek. Należy jednak pamiętać, że ten sam człowiek jest również ostatnim ogniwem, bo to dla niego podejmowane są działania. To on inicjuje zdarzenia i to on ostatecznie użytkuje ich efekty. Podczas mojej prelekcji chciałem udowodnić i uwypuklić znaczenie zespołu jako zbiór wiedzy, doświadczenia, różnych potrzeb i sposobu spojrzenia na stawiane mu zadanie jako gwarant prawidłowego i zgodnego z założeniami osiągniętego efektu. Każda komórka w organizacji ma inne potrzeby, inne ograniczenia i inne zadania. To dla tego istnieje potrzeba komunikowania się i uwzględniania interesów i potrzeb każdego działu. To w moim odczuciu pozwoli rozwijać się organizacji. Pozwoli uniknąć wielu trudnych sytuacji, a ostatecznie osiągnięty cel będzie spełniał pokładane w nim oczekiwania przy optymalizacji czasu i kosztów.