Współrzędnościowa technika pomiarowa charakteryzuje się strategią pomiarową odmienną od metrologii klasycznej. Celem prowadzenia pomiarów jest uzyskanie punktów o znanych współrzędnych. Zgodnie z definicją: „Współrzędnościowa technika pomiarowa – dziedzina zajmująca się pomiarem wymiarów geometrycznych. Celem pomiarów współrzędnościowych jest wyznaczenie wartości współrzędnych punktów badanego obiektu w założonym układzie współrzędnych. Idea tej techniki opiera się na założeniu, że badany element jest zbiorem prostych elementów geometrycznych, np. sfera, stożek, walec, płaszczyzna.” Współrzędnościowe maszyny pomiarowe (WMP), prawdopodobnie są najbardziej uniwersalnymi spośród dostępnych na rynku przyrządów pomiarowych. Maszyny te umożliwiają w szybki sposób, bez konieczności przezbrajania, dokonywać pomiarów wszystkich rodzajów wymiarów, które spotykane są w przemyśle, dzięki czemu mogą zastępować wiele przyrządów specjalnych. WMP zawsze współpracują z programem komputerowym, w którym można je programować w przyjaznym interfejsie użytkownika, zazwyczaj wykorzystującym programowanie dialogowe. Pomiary te, charakteryzują się pełną powtarzalnością, a także obiektywnością, ponieważ wpływ pomiarowca jest zmniejszony do minimum, w przypadku wykonywania w trybie automatycznym. Współrzędnościowa technika pomiarowa umożliwia dokonywanie oceny odchyłek, które wcześniej były niezwykle trudne do zmierzenia, albo wręcz niemożliwe. Do takich pomiarów należą np.:
- pomiary narzędzi skrawających, szczególnie do kół zębatych,
- pomiary kół zębatych (o zarysie nieewolwentowym, stożkowych, walcowych,
- ślimaków i ślimacznic),
- pomiary krzywek przestrzennych i płaskich,
- pomiary wymiarów oraz odchyłek kształtu i położenia elementów przestrzennych (np. jarzmo przekładni planetarnej).
Dzięki wykorzystaniu WMP można dokonywać pomiarów wszystkich wymiarów oraz tolerancji geometrycznych z jednego zamocowania w odniesieniu do jednego układu współrzędnych zgodnego z dokumentacją techniczną. Brak konieczności wykorzystywania kilku stanowisk pomiarowych, znacznie skraca czas kontroli części. Nie występuje konieczność dokładnie powtarzalnego mocowania, a także zapewnienia ustawienia elementu zgodnie z kierunkami osi maszyny, ponieważ każdorazowo w czasie wykonywania programu WMP bazuje się bezpośrednio na mierzonym elemencie i pracuje w lokalnym układzie współrzędnych. Pomiary prowadzone są na zasadzie określania relacji między elementami geometrycznymi takim jak: punkt, prosta, płaszczyzna, okrąg, walec, stożek, kula. Istnieje także możliwość kontroli profili i powierzchni swobodnych na zasadzie pomiaru odchyłki zarysu profilu i powierzchni.
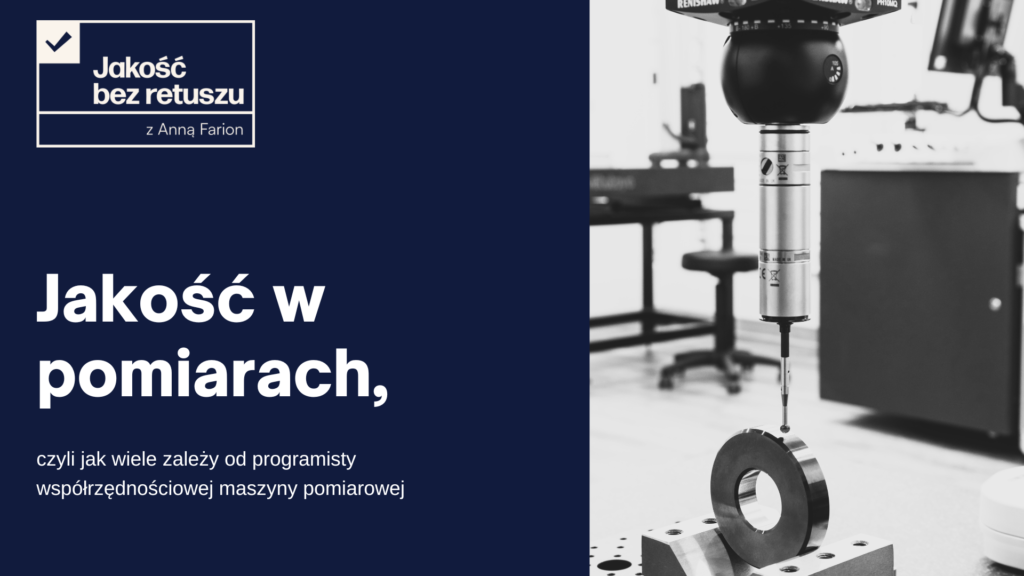
Często pomiarowcy są ostatnim ogniwem łańcucha tworzenia nowego produktu. W dniu dostawy otrzymują komponent i rysunek oraz niełatwe zadanie: zmierz. Pierwszym krokiem jest poprawnie zbudowany układ współrzędnych (ISO 5459), następnie sprawdzamy wymiary liniowe (ISO 14405) lub tolerancje geometryczne (ISO 1101), ale pamiętając o właściwej kolejności i sposobie odbierania stopni swobody (ISO 5459) oraz stosując bonusy wynikające z warunków maksimum materiału (ISO 2692), pamiętając, że profil i powierzchnia swobodna (ISO 1660) oraz szyki (ISO 5458) także rządzą się swoimi prawami. Bez norm GPS – Geometrical Product Specifications (ASME – GD&T), konstruktor nie miałby narzędzi, aby odwzorować montaż części w złożeniu. Programista współrzędnościowej maszyny pomiarowej musi jednak znać te same normy oraz mieć do nich dostęp każdego dnia swojej pracy, aby mógł przygotować program pomiarowy zgodny z założeniami konstruktora. Papier przyjmie wszystko, dlatego konstruktor powinien rozumieć zasady, które rządzą pomiarem. Musi dać programiście dobrą bazę i modyfikatory zastosowane w sposób właściwy i odzwierciedlający działanie części w złożeniu, aby wynik pomiaru jednoznacznie „mówił” za pomocą liczb: będzie pasować lub nie. Korzystajmy z dobrodziejstw norm GPS oraz współrzędnościowej techniki pomiarowej, ale róbmy to mądrze.
Najważniejsze normy, które pomiarowiec powinien znać chociaż z obrazków (kolejność jest nieprzypadkowa):
ISO 14405-1 – Tolerowanie wymiarów — Część 1: Wymiary liniowe wewnętrzne lub zewnętrzne
ISO 14405-3 – Tolerowanie wymiarów — Część 3: Wymiary kątowe wewnętrzne i zewnętrzne
ISO 5459 – Tolerancje geometryczne — Bazy i układy baz
ISO 1101 – Tolerancje geometryczne — Tolerancje kształtu, kierunku, położenia i bicia
ISO 1660 – Tolerancje geometryczne — Tolerancje profilu
ISO 5458 – Tolerancje geometryczne — Specyfikacje geometryczne szyku i łączone